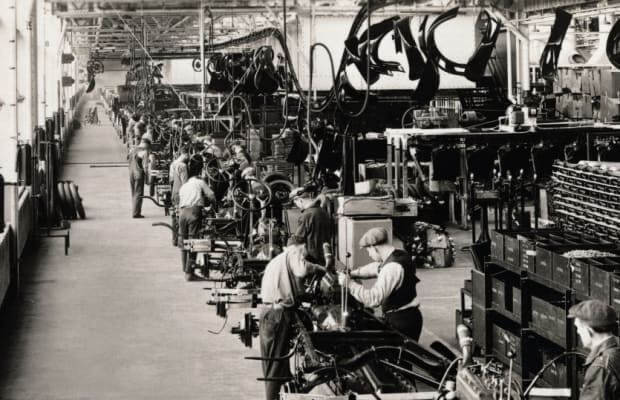
Ford Motor Company, despite the fact that it was founded in the early 20th century, is still one of the most famous and profitable companies in the sector. But such an extraordinary success would not have been possible without Henry Ford, an entrepreneur and inventor. Ford has always put a special focus on logistics issues as one of the foundations of the company’s development. There is definitely a lot to learn from the American pre-eminent entrepreneur in terms of logistics organisation.
Lesson One: Pay attention to stock levels
Henry Ford’s business has always been based on the principle of supply chain rationalisation. Any warehouse logistics issues should be solved quickly, efficiently, cheaply and without compromising the overall quality of service. At the time when Ford was just starting to develop, logistics was considered exclusively in terms of transporting and storing goods. Henry Ford changed the game rules.
Later, in his autobiography, the entrepreneur emphasised the importance of the smooth flow of parts and raw materials on the factory line, followed by the sale of finished cars in the shortest possible time. Ford believed that materials should not be stored in a warehouse for too long, including cars as the final product. However, you should not forget about buffer stocks of everything you need in case of force majeure. If the supply chain is disrupted for a period of time, such buffer stock will help to avoid downtime.
Lesson Two: Reasonable use of resources
To effectively increase the company’s profitability while reducing costs you should optimise processes. Henry Ford splendidly implemented this idea in his professional field. The first cars were extremely expensive and took a long time to manufacture. The entrepreneur decided to develop a car that would be affordable for almost everyone. He divided the construction of vehicles into stages, assigned each stage to a specific worker, and took the process of designing new cars to the assembly line.
Another optimisation solution to reduce the cost of manufacturing was to paint the cars exclusively black. This also influenced the scaling of the business. Subsequently, the ideas for optimisation were adopted by Taiichi Ohno, the executive of Toyota Motor Corporation. He formulated the following principles of logistics organisation:
- rational use of space;
- reduction of labour and time costs during product movement within the premises;
- encouragement of employee initiatives;
- Improvement of warehouse processes.
Lesson Three: Know how to delegate
Sometimes, you can learn even more from the mistakes made by great people than from successful solutions. Ford was forced out of the market by General Motors due to Henry Ford’s mistake, as he wanted to control absolutely every aspect of the company’s operations. Ford personally visited each coal and iron ore mine, inspected how the mechanisms worked, and checked the final result. In contrast, GM’s Alfred Sloan Jr. simply outsourced minor tasks. As time has shown, this approach is always more advantageous in the realities of a changing market. Later, even Ford himself adopted it.
There are many lessons to be learnt from the story of a prominent entrepreneur. But one of the most important is not to invent fundamentally new methods, but to optimise processes that already exist.